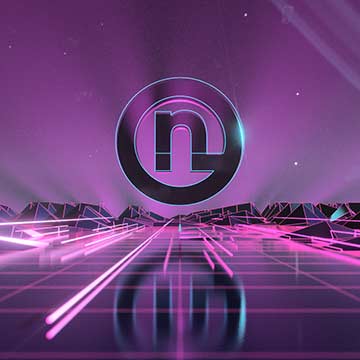
Why Innovation Matters
At Neuma Tattoo Machines, innovation isn’t just a buzzword—it’s a principle that drives every aspect of our tattoo machines. From precision engineering to the careful selection of materials, we’ve dedicated ourselves to creating tools that elevate the art of tattooing. In this blog, we’ll dive into the science behind Neuma tattoo machines and what makes them a cut above the rest.
Precision Engineering: Tolerance and Consistency
Neuma tattoo machines are primarily made from CNC-machined components, crafted with precision to meet exacting standards. Most parts are machined to a tolerance of five thousandths of an inch, with some even tighter—down to five ten-thousandths of an inch. To put that into perspective, the diameter of a human hair is approximately three thousandths of an inch. This means our components are machined with tolerances a minimum of just slightly larger than the width of a human hair.
In practical terms, if a part is designed to measure exactly a quarter of an inch but ends up being just six thousandths of an inch off, it will fail our strict quality control checks. This meticulous attention to detail ensures consistency across all our machines. When one machine performs flawlessly, you can trust that all of them will, thanks to the uniformity achieved through such precise manufacturing.
Materials That Stand the Test of Time
Material grade is another critical factor in manufacturing. For example, the aircraft-grade aluminum we use undergoes rigorous quality control to meet or exceed the strict standards we set for our manufacturers. All our materials—whether stainless steel, aluminum, or, in some cases, rare polymers—are carefully tested for durability, strength, wear resistance, and heat tolerance. This ensures that our components can withstand the demanding conditions without failing or deteriorating over time.
We go to great lengths to specify the exact materials we use. Additionally, we verify that their quality control processes align with our standards to maintain the highest level of reliability in our products.
We take material sourcing seriously—down to the manufacturer and region of origin—to ensure every component meets our exacting standards. This meticulous approach means Neuma tattoo machines can handle the tattoo artist’s needs without compromising performance.
CAD: Designing and Simulating Excellence
A significant amount of engineering goes into the design of all our components, especially the mechanism components. We use advanced computer software to design and generate parts, as well as to simulate motion and load on all interacting components. This allows us to pinpoint the center of mass for each moving part, reducing vibration while enhancing the force behind the needle’s hit.
Additionally, we simulate the stress on components like bearings and motor shafts to evaluate and maximize their lifespan. By identifying how much load is too much before breakdowns occur, we can engineer tattoo machines that do not exceed those limits, ensuring durability and consistent performance.
This commitment to thorough engineering translates into tattoo machines that run smoothly, efficiently, and reliably.
Prototyping and Real-World Testing
Before a Neuma tattoo machine reaches the market, it undergoes rigorous prototyping and testing phases. For instance, the Neuma 5 FLEX underwent more than a dozen mechanical revisions before we deemed it market ready. Many prototypes never make it to market because they fail to meet our high standards. At Neuma Tattoo Machines, we refuse to settle for anything less than perfection.
In addition to CAD design and computer simulations, we rely on prototyping and extensive real-world testing by our pro team to evaluate durability, usability, and performance. By involving professional tattoo artists, we ensure our prototypes are tested in real-life conditions over several months—sometimes up to a year—before deciding to move forward with a new product. This approach complements computer simulations, as real-world testing accounts for the variety of technical approaches used by different tattoo artists, which a simulation alone cannot replicate.
All components are 3D printed before we move to the prototyping stage. This allows us to refine and perfect our designs, eliminating unforeseen issues early on. Sometimes, we iterate on a single part ten to twenty times—or more—to ensure optimal functionality for the tattoo artist. For instance, with the cams, which need to be easily swapped out, we test numerous variations to determine the best possible design, guaranteeing ease of use and reliability.
Collaboration with Trusted Partners
At Neuma, we believe that Faulhaber is the world leader in miniature motors. Their motors are unmatched in durability, power, and high-speed performance, making them a trusted and reliable partner. Similarly, we consider Critical to be the leader in tattoo equipment battery packs. As a trusted collaborator, Critical not only provides exceptional products but also offers warranties to support the use of their battery packs.
We apply unwavering commitment to quality in our machine manufacturing process. while some companies might cut corners, we source only the best materials and components across the board. For instance, we use branded polymers directly from the originators—never generic versions—to ensure the highest standards of material quality. By prioritizing quality at every level, we guarantee that our machines are built with only the finest components.
Assembly and Quality Control
All final quality control checks, assembly, and testing are done in-house to ensure that every tattoo machine leaving our facility is in optimal operating condition. Each component is carefully hand-checked by a technician before assembly. Our motors undergo multiple inspections throughout the assembly process to ensure no issues arise at any stage. This thorough approach guarantees that every machine is in perfect working order and allows us to track our processes, making improvements whenever necessary.
Why Innovation Matters
As the Tattoo Industry faces consolidation, driven by venture capital and corporate interests, the focus often shifts away from artistry to profit margins. At Neuma Tattoo Machines, we’re committed to maintaining the integrity and performance of tattooing equipment by prioritizing quality, innovation, and functionality.
We believe that we have a responsibility to do our part to ensure that the aspects most important to the craft are maintained. We strive to keep the passion and craftsmanship alive in an industry increasingly dominated by large corporations.
When industries fail to innovate, they become dominated by cost-cutting measures and mass production. This leads to inferior products that prioritize profit over performance. At Neuma Tattoo Machines, we reject this trend. We believe that tattoo artists deserve tools that match their dedication to and their love for their craft.
Elevate Your Art with Neuma Tattoo Machines
Innovation is at the heart of everything we do. From the materials we use to the partnerships we forge, every decision is made with one goal in mind: to elevate your tattoo art. Experience the difference that Neuma Tattoo Machine’s cutting-edge technology can make in your tattooing journey.